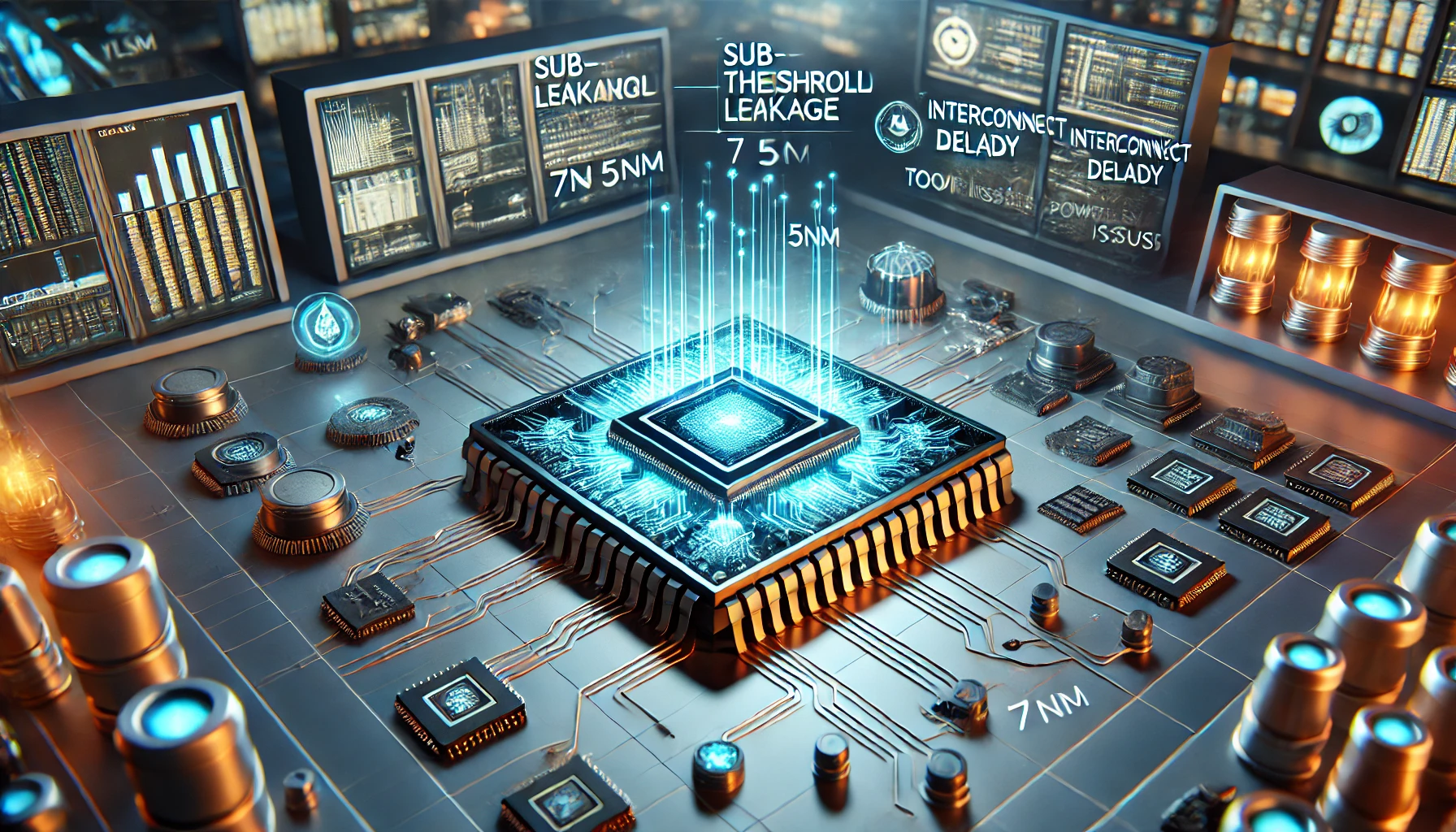
Challenges Faced By VLSI Industry in Today's Era
VLSI Challenges and Solutions
VLSI Challenges and Solutions
Sub-Threshold Leakage and Power Integrity
In the ever-evolving landscape of VLSI design, managing sub-threshold leakage and power integrity has emerged as a critical challenge, particularly at advanced process nodes such as 7nm and 5nm. As transistor sizes shrink, the threshold voltage (Vth) must be reduced to sustain switching speeds. However, this reduction leads to an exponential increase in sub-threshold leakage currents, contributing significantly to static power dissipation—an especially pressing issue for battery-operated devices like mobile phones and IoT systems. Moreover, densely packed power grids in modern SoCs introduce power integrity concerns, such as IR drops and noise, which can result in insufficient voltage delivery to critical components, causing functional errors or timing violations. The impact of these challenges is profound, creating a delicate trade-off between performance and energy efficiency. Addressing them requires a multifaceted approach. Techniques such as Multi-Threshold CMOS (MTCMOS) optimize leakage by employing transistors with varying threshold voltages across critical and non-critical paths, while power gating cuts off power to idle modules, reducing static power consumption. Furthermore, Dynamic Voltage and Frequency Scaling (DVFS) dynamically adjusts operating conditions to match workload demands, balancing energy efficiency and performance. Finally, robust power grid designs, incorporating redundant delivery paths and decoupling capacitors, are essential to mitigate IR drop and ensure reliable voltage supply. Together, these strategies pave the way for more efficient and reliable chip designs in the face of shrinking geometries and rising power demands.
Interconnect Delay and Signal Integrity
As transistor switching speeds continue to improve with process scaling, the delay caused by interconnects has emerged as a critical bottleneck in modern VLSI designs. At smaller process nodes, the physical dimensions of interconnects shrink, increasing their resistance (R) and capacitance (C). This results in pronounced RC delays, where signal propagation becomes significantly slower compared to logic gate delays. In complex designs with high-density routing or high operating frequencies, these delays can lead to severe performance limitations. Adding to this challenge are signal integrity issues, such as crosstalk and electromagnetic interference (EMI). Crosstalk arises from unwanted coupling between adjacent interconnects, leading to glitches, noise, or incorrect logic transitions. EMI further exacerbates these problems, especially in high-speed designs, where precise timing is essential. Together, these factors make achieving timing closure—a crucial step in digital design—particularly difficult in advanced SoCs, especially those with extensive interconnect lengths or complex routing paths. To address these challenges, a range of effective strategies has been adopted. The use of low-k dielectric materials reduces capacitance in interconnects, thereby minimizing RC delays and overall power consumption. Shielding and spacing techniques involve introducing shielding lines and optimizing spacing between critical signals to reduce crosstalk. Additionally, buffer insertion along long interconnects restores signal strength and reduces propagation delays. Advanced routing optimization using EDA tools ensures timing-driven placement and layer assignment, mitigating the impact of RC delays. These solutions collectively enable the development of high-speed, high-density designs while maintaining signal integrity and performance.
Design for Manufacturability (DFM)
Design for Manufacturability (DFM) is a critical consideration in the VLSI industry, particularly at advanced process nodes like 7nm and below, where the challenges of patterning push the limits of traditional lithography. At these scales, the features on a chip are smaller than the wavelength of the light used in photolithography, leading to significant issues such as line-edge roughness, pattern distortion, and overlay errors. These problems are exacerbated by variations in manufacturing processes, including systematic defects like etching irregularities and random defects like particle contamination. Together, these factors reduce the manufacturing yield, driving up the cost of chip production and complicating the already intricate fabrication process. To address these challenges, several advanced techniques are employed. Optical Proximity Correction (OPC) modifies mask layouts to counteract distortions during the lithographic process, ensuring better pattern fidelity. Double and multi-patterning techniques split complex patterns into multiple masks, enabling more accurate patterning despite lithographic limitations. Integrating DFM-aware design practices early in the design cycle allows potential yield issues to be identified and addressed proactively, minimizing late-stage corrections. Additionally, adopting regularized, gridded layouts simplifies compliance with stringent design rules and improves overall manufacturability. These approaches collectively enable the successful production of defect-free chips, ensuring both high yield and cost-effectiveness in advanced semiconductor manufacturing.
Variability and Reliability at Advanced Nodes
At advanced process nodes, variability and reliability pose significant challenges that directly impact chip performance, yield, and longevity. Process variability arises from inconsistencies in key transistor parameters such as threshold voltage, channel length, and oxide thickness, which are exacerbated by phenomena like random dopant fluctuation (RDF) and line-edge roughness. These variations lead to unpredictable transistor behavior, complicating the design of robust and high-performance circuits. Simultaneously, reliability issues become more pronounced as device dimensions shrink. Aging effects, such as negative bias temperature instability (NBTI) and positive bias temperature instability (PBTI), degrade transistor performance over time. Other critical concerns, like electromigration (metal erosion due to high current density) and time-dependent dielectric breakdown (TDDB) (failure of insulating layers), threaten the structural and functional integrity of the chip, reducing its operational lifespan. To address these challenges, advanced design and verification techniques are employed. Adaptive body biasing dynamically adjusts transistor threshold voltages to counteract variability effects. Redundant design strategies introduce backup circuitry in critical paths to ensure reliability even in the event of failures. Reliability stress testing during design verification identifies weaknesses under worst-case conditions, enabling preemptive solutions. Additionally, incorporating error correction mechanisms like error correction codes (ECC) and fault-tolerant architectures enhances robustness in memory and critical data paths. These solutions collectively enable the design of reliable and high-yield chips, even under the stringent constraints of advanced semiconductor nodes.
Ecosystem Fragmentation and Tool Integration
It is a significant challenge in modern VLSI design, particularly for complex system-on-chip (SoC) architectures. These designs often rely on multiple third-party IP cores, such as memory controllers and communication interfaces, alongside a wide array of electronic design automation (EDA) tools for both front-end and back-end workflows. Each IP block and toolset comes with its own specifications, constraints, and compatibility requirements, making seamless integration a daunting task. Ensuring that an IP block from one vendor aligns with another or fits into the overarching design flow can be time-intensive and error-prone. Moreover, the fragmentation of tools across different phases of the design process—such as synthesis, placement, and routing—can result in inconsistencies and necessitate extensive manual intervention. These integration challenges can delay time-to-market and inflate costs, posing significant risks in a competitive industry. To overcome these challenges, a structured approach is essential. Standardized interfaces, like AMBA and AXI, ensure interoperability and simplify IP integration, with compliance testing verifying seamless operation. Unified design platforms, such as those offered by Cadence or Synopsys, provide end-to-end solutions that streamline the design and verification process, reducing fragmentation. Continuous integration (CI) workflows automate testing and integration of IPs, catching potential issues early and maintaining design cohesion. Finally, fostering cross-functional collaboration among design, verification, and physical implementation teams prevents workflow silos and ensures a cohesive development environment. These strategies enable smoother tool integration, faster development cycles, and robust designs, addressing the complexity of today’s VLSI ecosystems.
Reviews